How Autonautics helped companies manage fleet and delivery on time during the pandemic?
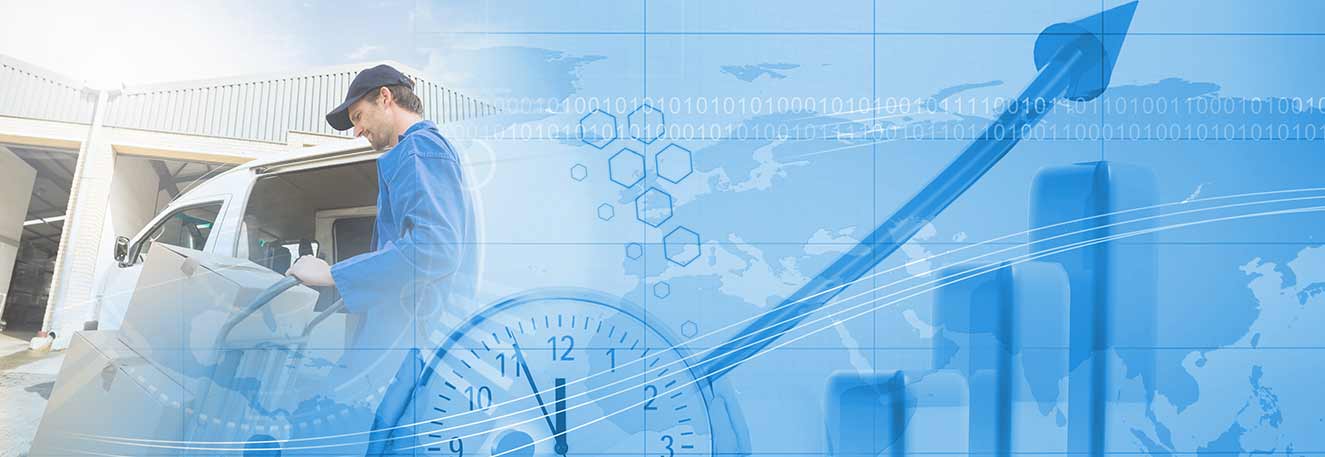
1. Constantly monitoring warehouses and mobile assets to ensure there is no deterioration of product quality
They monitor temperatures round-the-clock in both warehouses and trucks. Smart sensors immediately send alerts of irregularities. They identify the issue and resolve it right away, so bigger problems are effectively prevented. Smart warehousing has prevented spoiling of products and subsequent wastage.
Remote monitoring is a blessing in disguise, especially during the Covid-19 pandemic when physical distancing is the need of the hour. Supply chain responsiveness has got a significant boost as they can easily track inventory items with status and position in real time. It has minimized revenue leakage due to safe storage, transportation, and on-time delivery.
2. Ensure safety of drivers while they are out making deliveries
Supply chain management falls apart without timely delivery, which in turn depends upon the efficiency of drivers and well-optimized routes. With the aid of real-time information using synchronized alerts, they are able to monitor driving patterns, and find out about unsafe driving behaviour as well. Using preventive analysis and predictive maintenance, they can devise prescriptive actions accordingly.
3. Maintaining Covid-19 safety protocols while ensuring smooth operation
Following hygiene and physical distancing protocols is fine, but the threat of getting infected still remains for drivers who take that risk each day. Using Connected Logistics, they are able to chalk out a safe route for drivers travelling interstate. They have access to maps detailing containment zones and hence can mark Covid-19 affected warehouses – the data is sent to drivers so they know which places to avoid.
4. Maintaining customer satisfaction and on-time delivery
As mentioned, supply chain management won’t exist without timely delivery, which affects customer satisfaction. By monitoring performance of vehicles in their fleet, they have been able to detect problem areas such as common causes of truck breakdown. It has allowed them to predict patterns and make informed decisions regarding maintenance, so customer satisfaction and timely delivery is always guaranteed.
5. Maximize asset usage
It is imperative to understand how vehicles are being used and identify areas of imbalance, which can keep your business moving and manage costs effectively. It is about using the fleet to its fullest potential, so vehicles can be adapted to changing business needs. Drive time, mileage, days driven, etc. are some of the parameters that can be used to determine asset utilization. You can check out the vehicle statistics via the telematics system – they can be used for rotating vehicles for service requirements to manage downtime, understand how conditions impact trip distance, and identify vehicles that can be repurposed for other revenue streams.
“Thanks to Anstel’s highly integrated secure data analytics, robust Euro made devices, and 24 x7 customer support, we are functioning like a well-oiled machine”